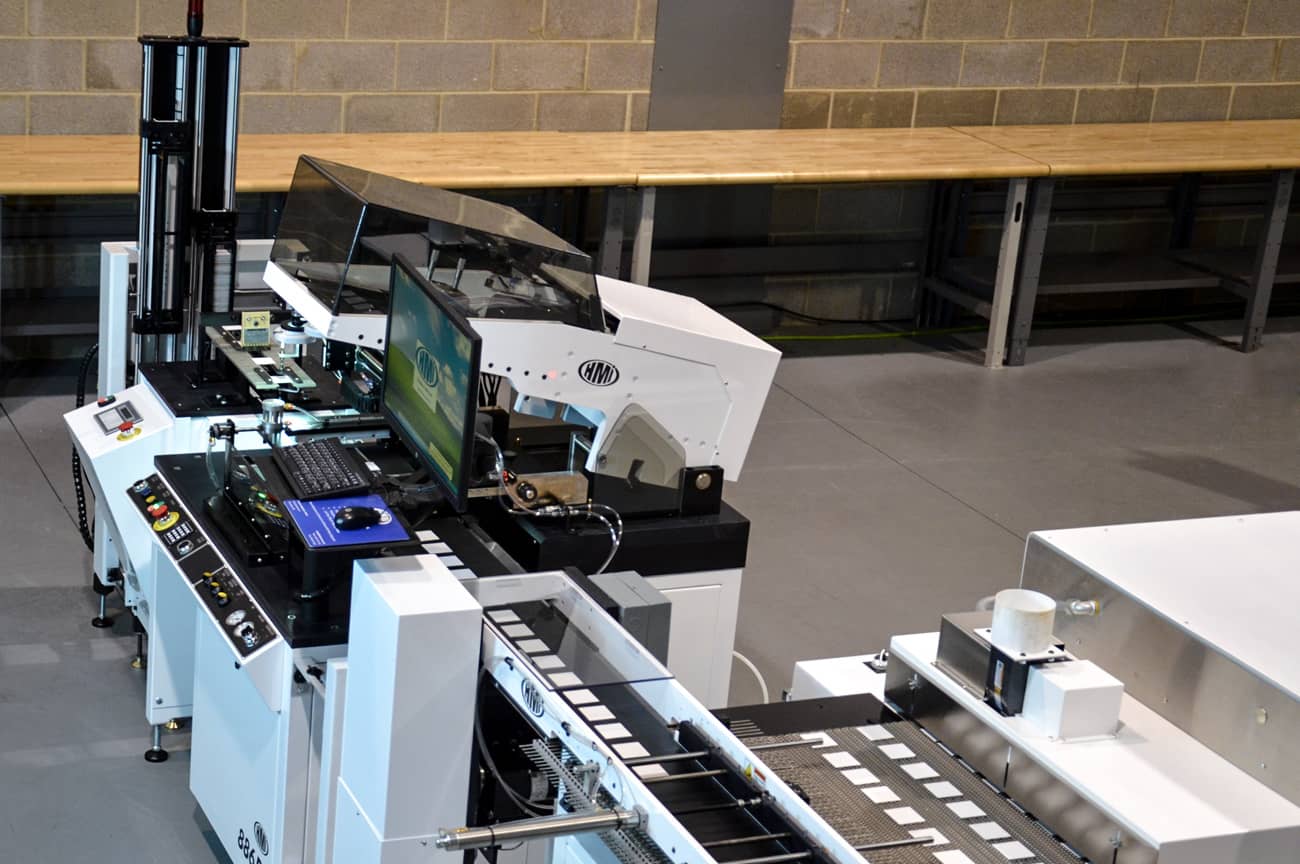
Featured Solution
Fully Automated Screen Printing Systems
Expand your manufacturing capabilities with a complete line automation solution from HMI. Our automated screen printing systems are available in semi-automatic or fully-automatic lines according to your specific application. These systems offer simple setup, user-friendly design, and industry-standard precision deposition.Learn More
Hary Manufacturing Inc.
Lebanon, NJ 08833
(908) 722.7100